ジグ設計の基本~工程設計とワーク特性を把握した位置決め~
はじめに
ワークをマシニング加工する場合、次の2つが重要になります。
- 図面精度が確保できるように工程設計
- ワークの特性に合わせて位置決めポイントを設定
図面精度、ワークの特性を理解せずに工程設計や位置決めを行うと、
位置決め精度のばらつきや精度が確保されないといった不良につながります。
そのため、工程設計する場合は次の2点が必要です。
- 図面精度をよく理解し最適な加工方法を選択
- ワークは必ず現物と図面を照合し安定した位置決めができるようにする
ここでは、「図面精度に合わせた工程設計とワーク特性を把握した位置決めの必要性」に関してわかりやすく解説しています。
加工工程の設計
加工工程を設計するには図面精度をよく理解することが重要です。
ここからは、工程設計の考え方や手法について例をもとに解説していきます。
加工面を確認し工程数を検討する
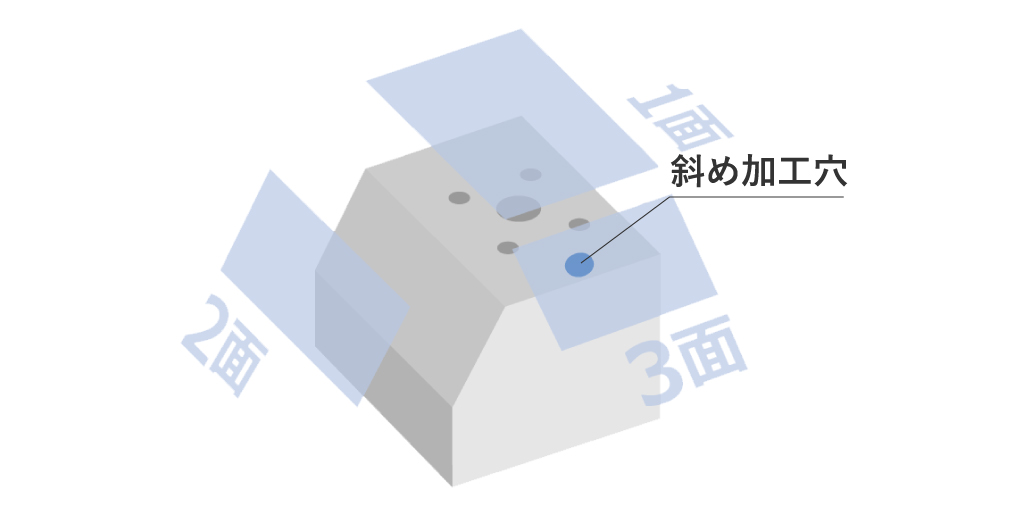
加工部位を面として捉えて、何面あるかを確認することで工程数を検討することができます。
ワークの加工面数量、図面標記精度の場所などを確認し工程を設計していきます。
図面精度をもとに工程数を決定する
次に確認する点は「図面中の幾何交差を明確にする」ことです。お互いの面の関係は幾何公差で確認を行い工程数を決めます。
特に、同軸度又は直角度等で高精度が求められる場合は、以下を考慮して工程数を決める必要があります。
直角度、平行度、穴径、穴ピッチなどが高精度な場合 | :荒加工、仕上げ加工の工程分け |
---|---|
同軸度、対称度などが高精度な場合 | :段取り替えを行わない横形マシングセンタや5軸加工機などで割り出し同時加工 |
工程の決め方
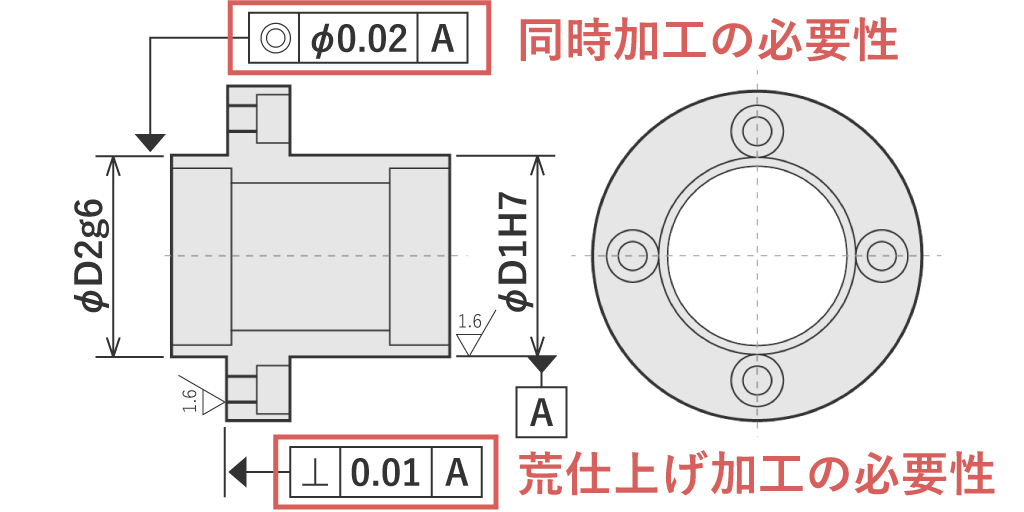
・直角度0.01 ・・・荒加工後に仕上げ加工で精度を確保
ワークの特性を把握した位置決め
加工工程の設計に加えて次に確認する点は「ワークの特性をよく理解すること」です。
ここからは、ワーク特性を理解する必要性と工程設計に合わせた位置決めの考え方について解説していきます。
図面と現物素材を照合する
ジグを検討する前に最も重要なことは「加工するワークの現物を図面と照合し確認すること」です。
これは素材図面などに表記されていないワークの癖や寸法のバラつきや整合性を現物で確認するためです。
確認する点は以下のようなものがあります。
図面とワークの整合性 | :現物と図面は同じか、設計変更前の古いものではないか |
---|---|
素材の形状特性 | :抜き勾配はどの程度か、図面に明示されているか |
素材支給の状態 | :パーティングラインの場所、バリの状態、増殖に対する対策方法 |
位置決め基準の設定
工程設計、ワークの特性を理解をしたら位置決めのポイントを明確にしていきます。
1工程目で加工する基準がその後の加工精度に大きく影響するため、1工程目のジグがすべてのカギを握るといっても過言ではありません。
ここからは工程ごとの基準のつくり方を解説していきます。
1工程目の基準
1工程目の加工面は、2工程目以降の基準となるため歪みが発生しないように加工しなければなりません。
しかし、1工程目は黒皮素材のため、どの位置で位置決めするか以下のポイントを押さえることが重要です。
1工程目の黒皮基準で押さえるポイント
図面中に基準表示のされている場所 | :ワークに求められる寸法や精度の基準となるため1工程目に加工する |
---|---|
図面上の寸法線の出発ポイント | :出発点からの寸法・精度が必要となるため1工程目に加工する |
安定した平面のある場所であること | :バラつきが少なく安定するため位置が決まりやすい |
型割面のパーチングライン付近を避けた場所 | :パーチングラインはバリがありバラつくため位置決めポイントに適さな |
できるだけ同じ割型面になる場所(特に受け面) | :位置決めポイントに割型面が合致しないようにする |
基準用の捨て加工 | :2工程目の加工に際して基準が取れない場合、加工しても問題ない場所に基準をつくる |
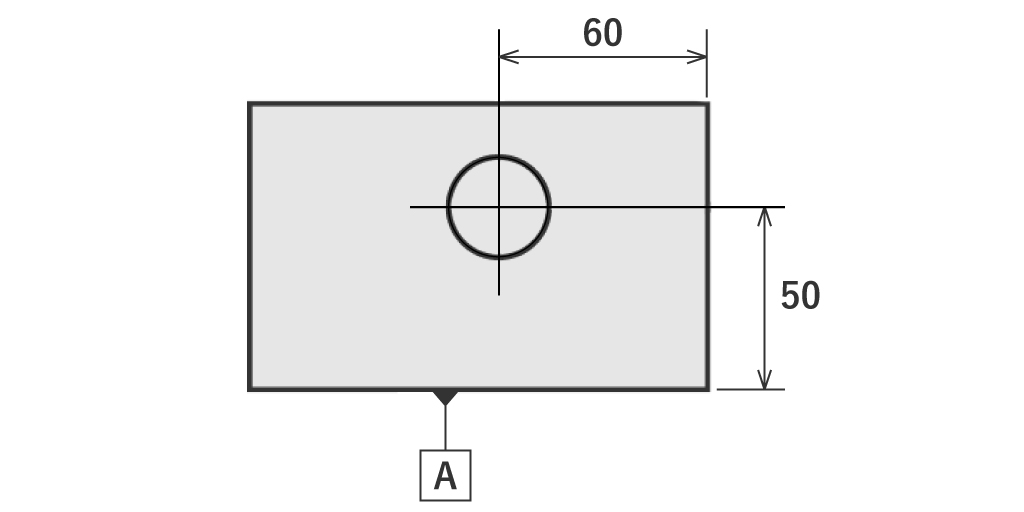
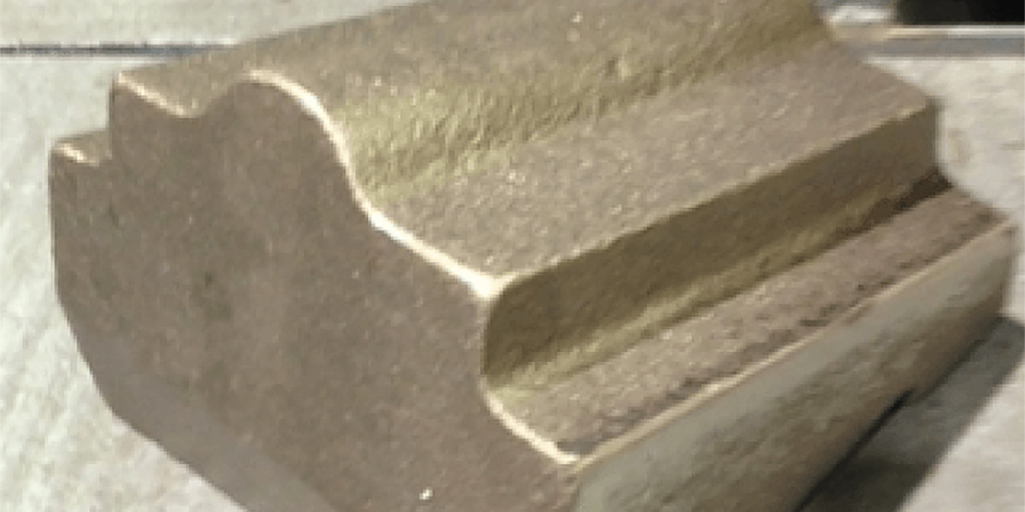
2工程目以降の基準
1工程目で加工した部位を基準にして2工程目の基準を設定します。
2工程目以降は1工程目で加工した部位を基準にするため以下のポイントを押さえることが重要です。
2工程目以降の基準で押さえるポイント
1工程目で加工された面又は穴を利用する | :1工程目の加工部位が基準となるため位置決めにする |
---|---|
多工程ある場合はできるだけ基準を統一する | :基準を増やすとそれだけ製品精度がバラつくため少なくする |