位置決めの基本~加工負荷と位置決めの配置~
はじめに
機械加工を行う際、様々な方向から加わる加工負荷で、ワークに加工歪みが発生していませんか?
加工方向を考慮して位置決めを配置しないと、ワークが加工負荷によって歪み、寸法、平行、直角などの精度が悪化します。
また、加工によって発生した切粉がワークや位置決め部に付着したままの状態で加工を行うと、
ワークに傷がつく、精度不良などの悪影響を及ぼします。
これらの影響を最小限に抑えるためには、
- 加工負荷によってワークが動きにくい位置決めの配置を行う。
- 切粉が付着しにくい位置決め形状にする。
など加工状況に応じて位置決め方法を工夫することが必要です。
ここでは、加工条件や状況に合わせた位置決めの使用方法についてわかりやすく解説しています。
加工負荷の方向に合わせた位置決め方法
位置決めの配置には、「加工負荷に合わせて配置する方法」があります。
これは、加工負荷の加わる方向に対して、受け側となるように位置決め部品を配置する手法です。
加工方向に対して位置決めを配置することにより、位置決めに加えてストッパーとしての役割を担うことができます。
加工内容別に配置方法について解説していきます。
フライス加工の位置決め配置
フライス加工をする場合、主軸を送る方向と回転方向に加工負荷が加わります。
この場合、以下の手法をとることで、位置決めに加えてストッパーの役割を担うことができます。
ワークの安定には位置決めの内側を加工するで安定
加工方向に対して位置決めを配置することでストッパーの役割を担えます。
ただし、加工位置によってストッパーの効果は大きく異なります。
加工位置が位置決め位置よりも外側になってしまうと、ワークに回転方向の力が加わり不安定な状態となります。
この場合、位置決めの3点の三角形を大きくし位置決めの内側を加工できるように配置することで、加工負荷に対して安定させることができます。
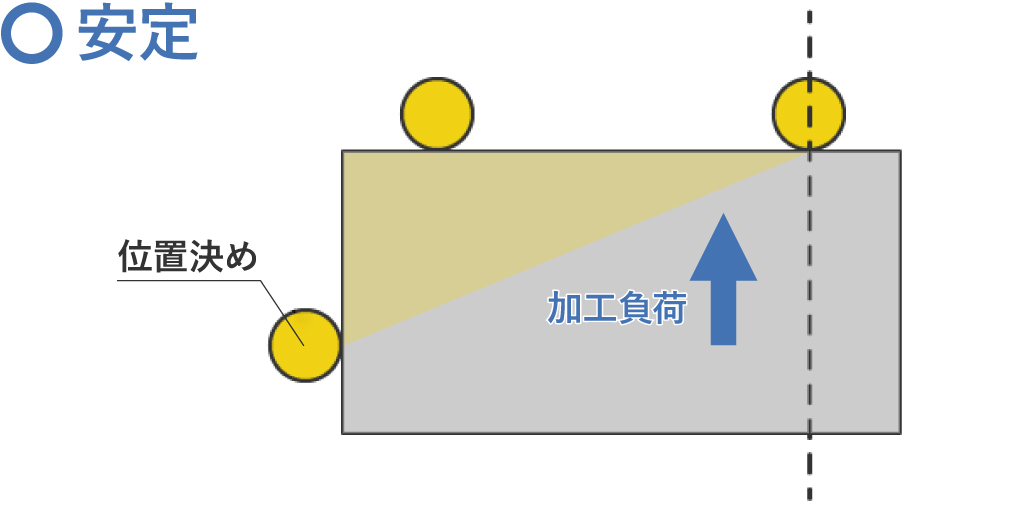
加工負荷を位置決めで受けることができる
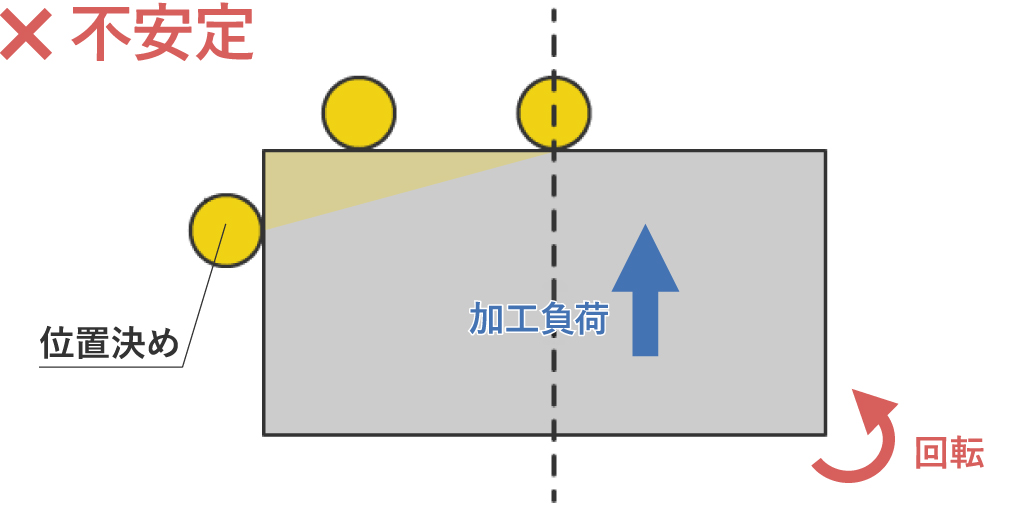
位置決めの三角形が小さく安定していない
ドリル加工の位置決め配置
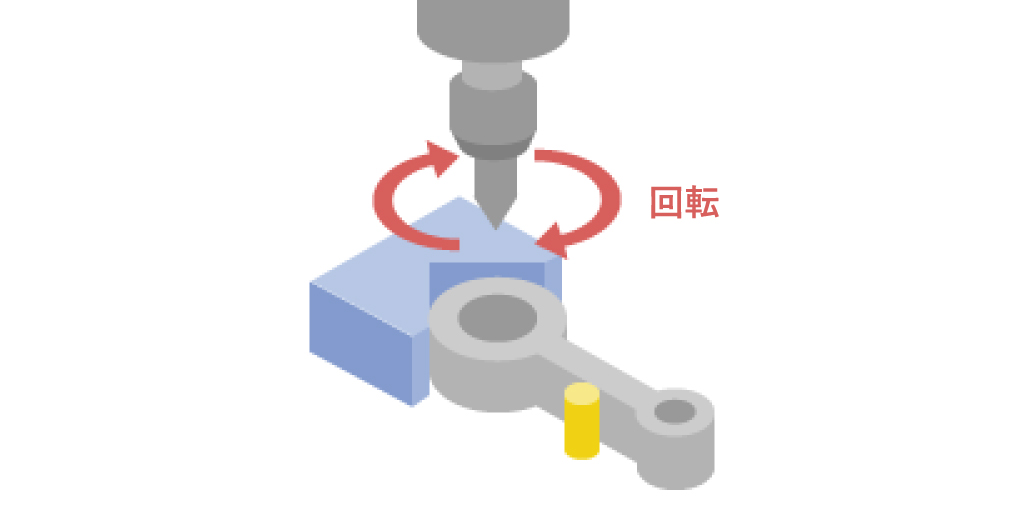
この場合、ワークが共回りしないように回転方向に対して位置決めを配置することで、位置決めに加えてストッパーの役割を担うことができます。
ワークの上面に加工負荷が掛かる場合の位置決めの配置
位置決めを配置する場所はワーク箇所や方向を考慮します。
位置決めと加工箇所を近づけることで、加工部位に対するワーク剛性を上げることができ、加工精度の向上やビビリ対策にもつながります。
以下のように、加工箇所を考慮した場合、Aパターンの位置決め配置の方が加工に対する変位を小さくすることができます。
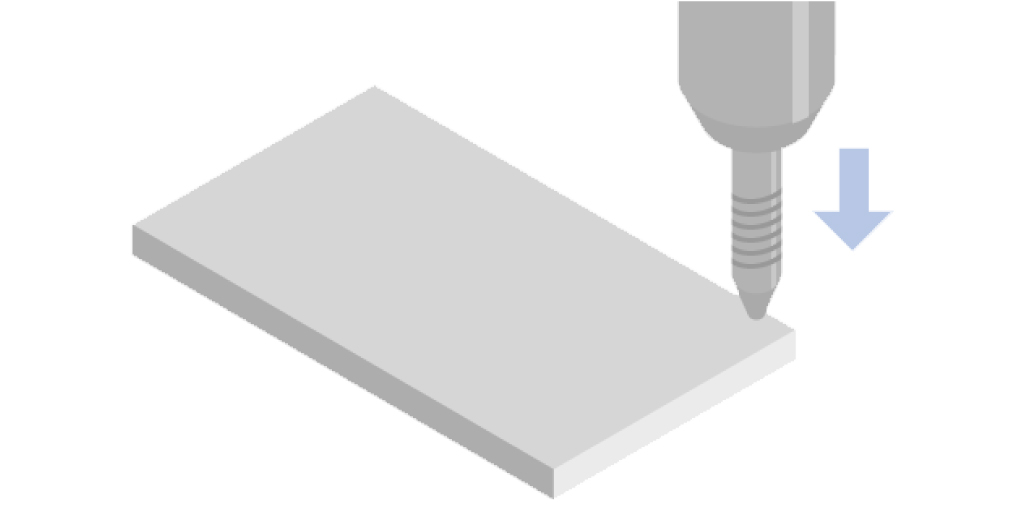
切粉が付着しにくい位置決め形状
位置決め部はワーク位置の原点になります。切粉が付着した状態で位置決めすると精度がばらついてしまいます。
これらを回避するには、ワークを取り外した際に切粉や切削水が位置決め部に付着しにくい形状にすることが重要です。
基準面を小さくして切粉を付着しにくくする
高さ方向の位置決め部が同一平面の場合、加工によって発生した切粉が残り位置決め部に付着する可能性があります。
この場合、ワークが接触する部分のみを嵩上げしワークの内側に入れることによって切粉の付着を防ぐことができます。
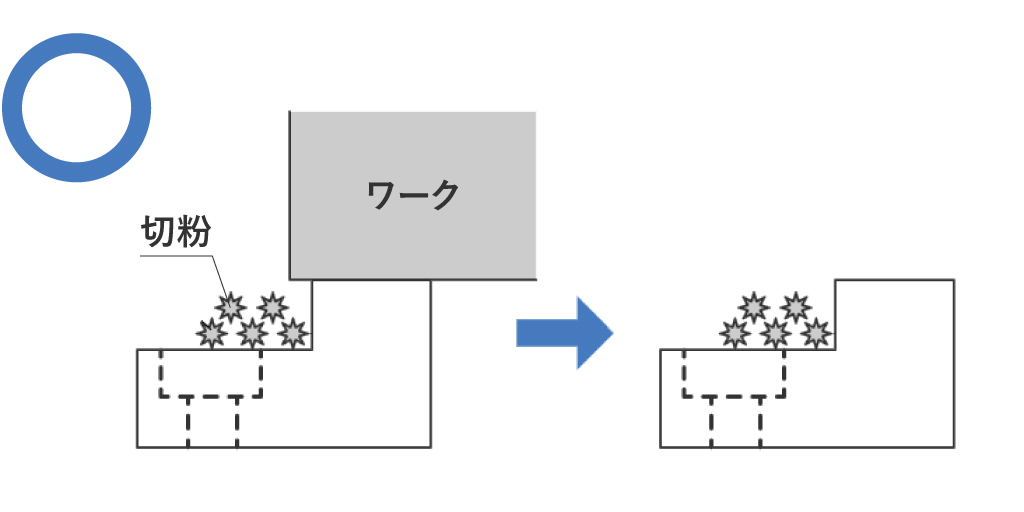
基準面以外の面を低くして切粉堆積の影響を受けにくくする
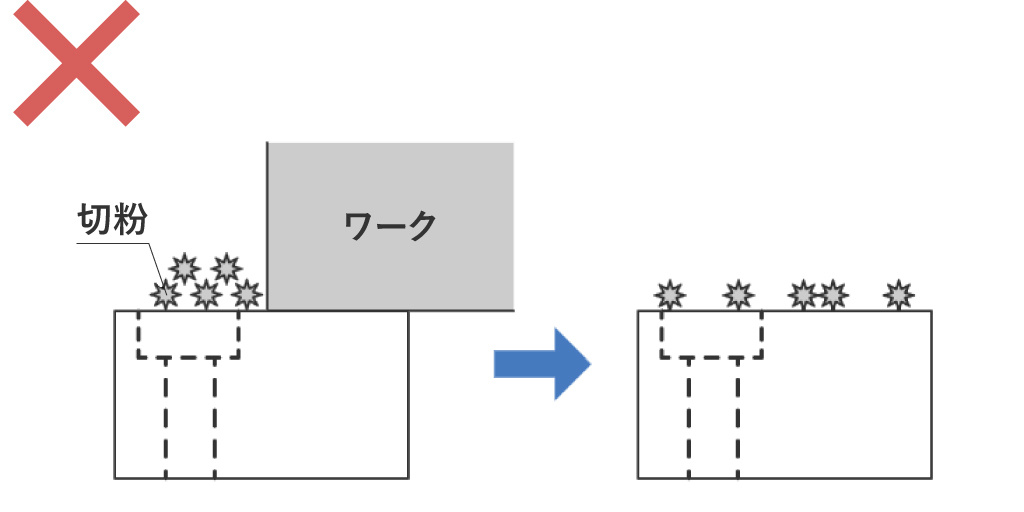
切粉が基準面に残りやすい
直角部に切粉の逃がしスペースを作り付着しにくくする
位置決め部が直角面の場合、切粉や切削水が入り込むと位置決め部との密着不良につながります。
このような場合、位置決めの配置や溝を設け切粉や切削水の逃がしスペースを作ることで付着を防止することができます。
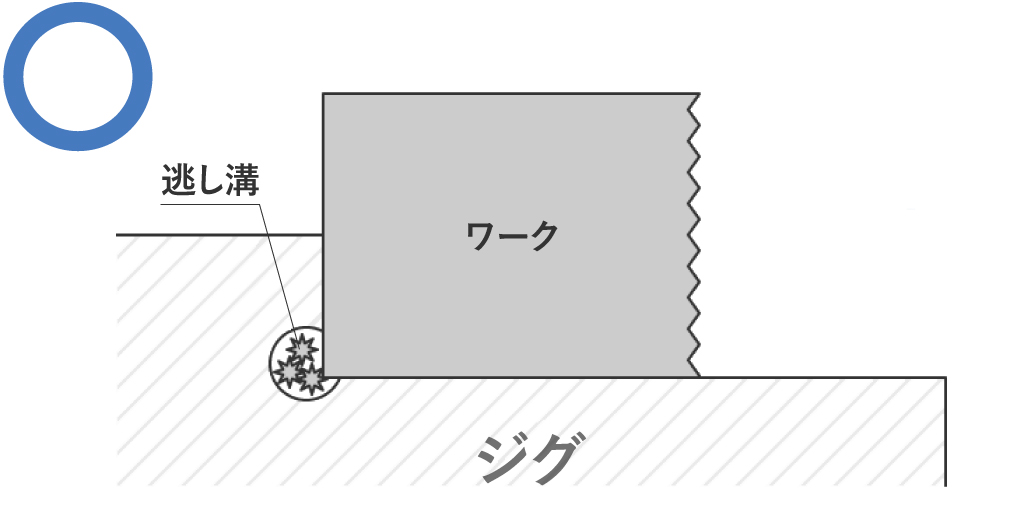
ワークの角が干渉し難い
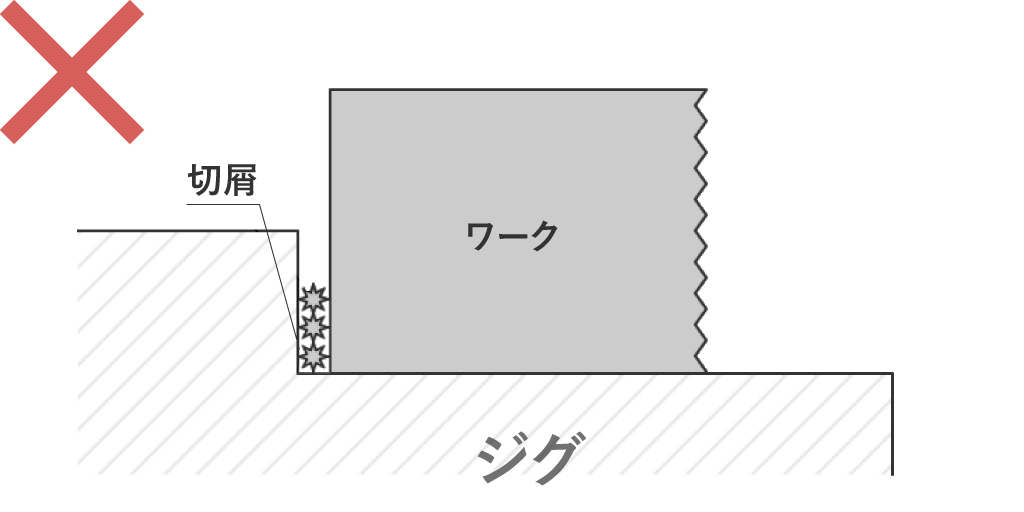
位置決めを追加して逃がしスペースを確保している
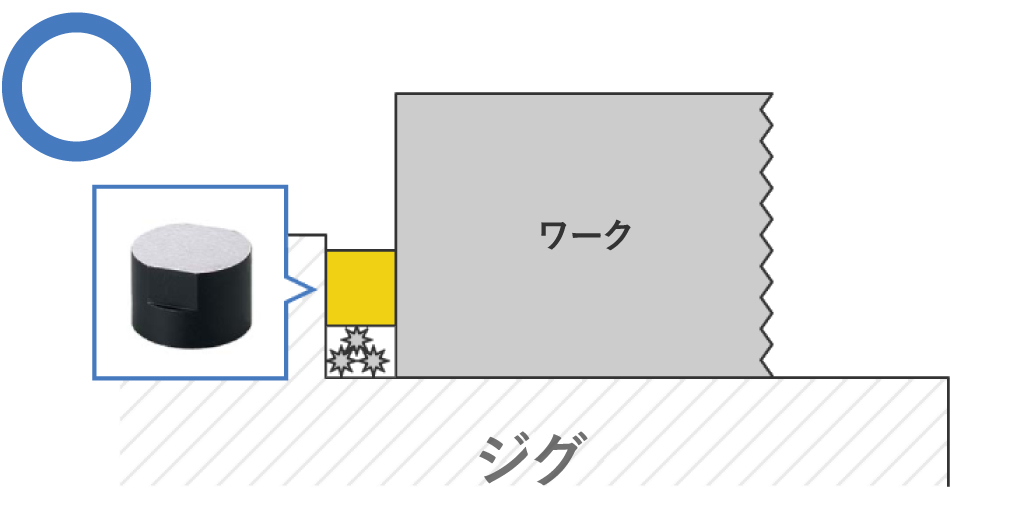
密着不良が起きやすい